It is with great joy that it can be reported that the main stabilization work on Viking is finished! With the visit to our ship by our primary consultant Gunnar Eldjarn in August, 2016–first to evaluate the work that had been done and then make recommendations for how to proceed–we made our final plans and carried out their implementation. It was especially gratifying to hear Gunnar as he inspected the new “pillows” providing a cushion between the metal support jacks and the ship, proclaiming them either “very good” or “excellent.” Gunnar agreed that we could use the screwjack idea for both the bow and stern supports, though the bow jack could be less robust to minimize its visual impact, and said that where the jack touches the keel there needs only to be four inches of material to provide adequate support. Gunnar also agreed that getting the mast off the ground and on display supported by the ships cradle made good sense and thought that having the yard alongside the mast would be helpful. He commented on our two tone color scheme of gray below and black above and how it complements the ship, and was pleased to hear that we would be soon completing what remained unpainted.
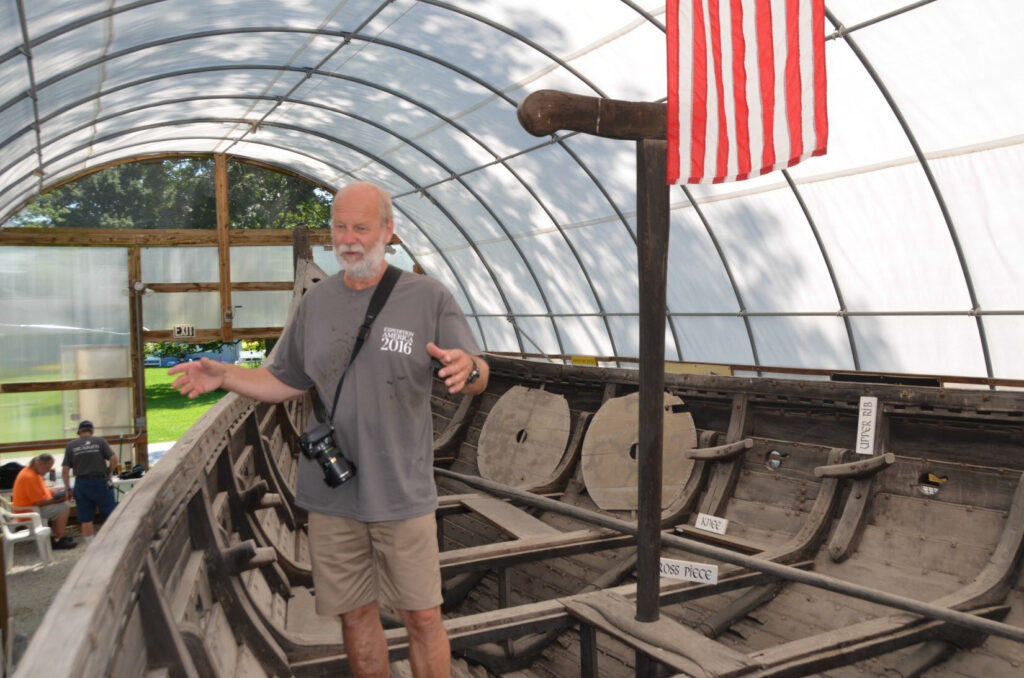
Starting in late September and continuing into mid-November, Bruce Andresen worked with Neil Anderson, Dave Barrows, Dave Nordin, and Perry Straw at the ship to remove old parts, modify existing parts and add new parts to accomplish these goals and to prepare for winter. On October 15th we were joined by Roar Broch, Andrew Woods, Jeff Rydin, Jamie Larson, and Dan Snyder of “Mast Movers LLC” (also the caretaker of Good Templar Park), who all helped to move the mast to its new home atop the cradle outriggers. Thanks to the aid of Dan’s tractor, moving the 52-foot-long mast was less of a back-breaking effort than anticipated, but we now all have a healthy respect for the strength of the Vikings of old who could raise and lower it with the limited tools and technology they had available to them!
After the mast move, work continued through early November to finish the projects for this year. Here is a summary of what has been accomplished:
- Added bow and stern jacks per directions from Gunnar Eldjarn
- Moved the mast and yard to their permanent location on the starboard outriggers
- Lined the starboard side of the shelter with plywood to cut down on dust, wind and snow
- Removed the cables inside the ship as they are no longer needed and compromised the view of the ship
- Removed part or all of the original ship supports on the starboard side
- Corrected the bow tent support
- Removed the tent support at the mast to be corrected in the spring
- Painted all bare metal that was added to the cradle
- The shelter cover was replaced with a temporary (till mid next year) cover, thanks to Peter Orum.
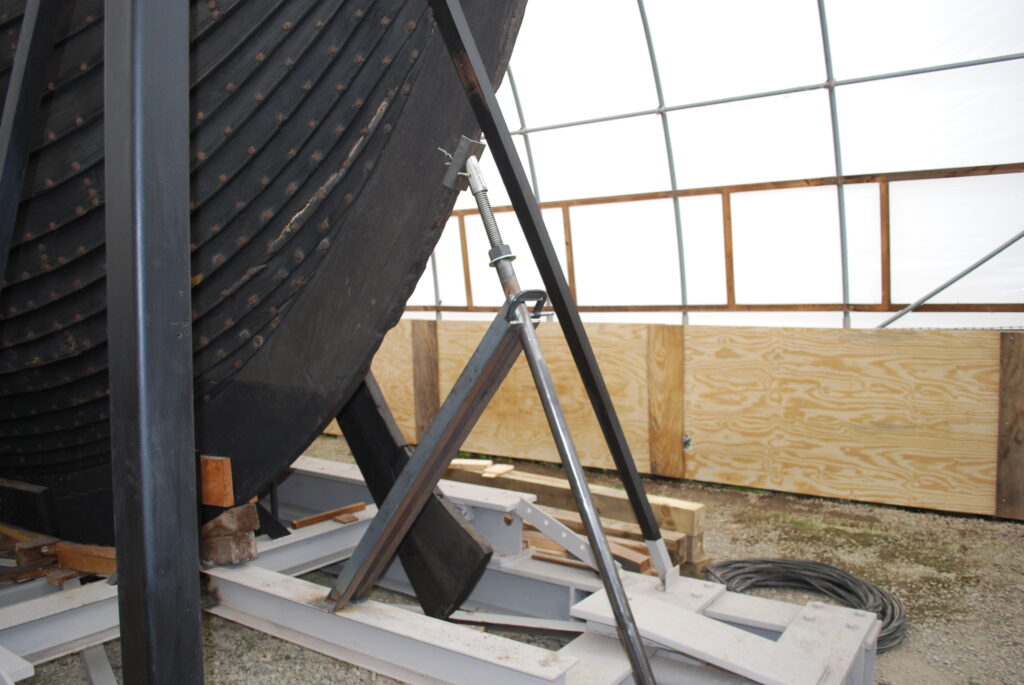
Many thanks go out to all who have contributed their time, sweat and energy to helping us stabilize Viking’s condition and provide her with the best structural support she’s had since she left the water!